Critical data collected at highway speed
By Jeff Winke
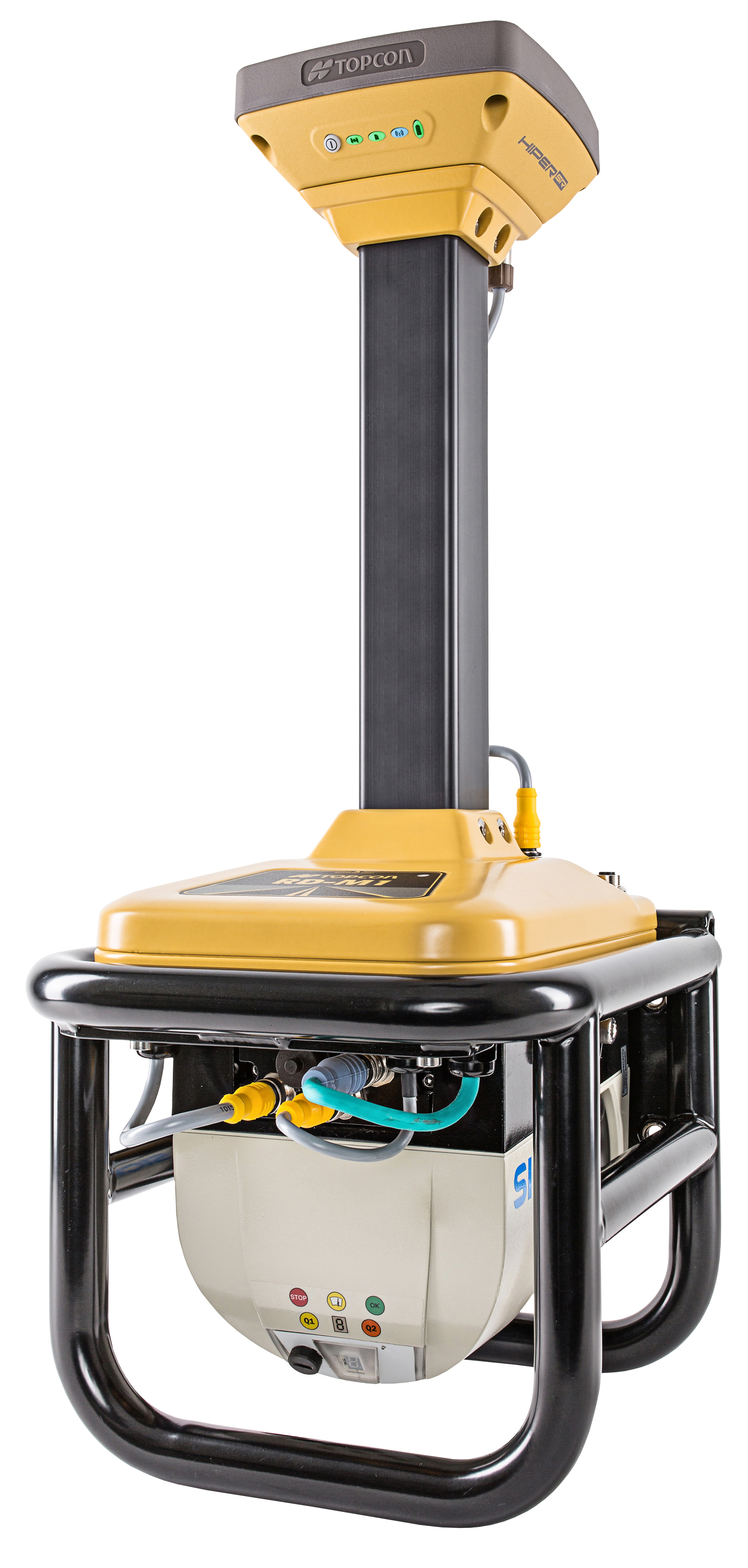
Traditionally, highway resurfacing projects have been a challenge, not only for the contractor, but the inconvenienced community through which the road passes. To collect the project data needed to perform the resurface, typically required lane closures and a team of surveyors collecting data points from along the side of the road with diverted traffic whizzing past. It was a slow, cumbersome, and dangerous process, that affected the daily commuter flow and affected the contractor’s project timeline.
But things are better.
Designed to work at the speed of highway traffic, the Topcon SmoothRide resurfacing system is intended to safely assist road resurfacing contractors without the need for road or lane closures. The system is fully automated with GNSS and sonic tracker control. It is designed to deliver accurate thickness boundaries while maintaining projected yield. It eliminates the need for survey strings, averaging skis, and lasers.
“In most situations, it’s inconvenient or impossible, to shut down a road and map its surface using traditional point-to-point surveying methods,” says Murray Lodge, senior vice president and general manager of the Topcon Positioning Group Construction Business Unit. “We’ve developed a way to scan roads at highway speeds with no need for lane closures, crash trucks, escorts or any other typical road survey collection obstacles. With the new RD-M1 scanning unit, the system maps the existing surface elevations — with many more points captured versus what can be expected with traditional tools — providing more accurate data needed to confidently estimate materials, as well as form the basis of the final design surface.”
The SmoothRide system uses a Topcon RD-M1 (Realistic Dimension – Mapping One) Road Resurfacing Scanner that is attached to a vehicle, typically a pick-up truck. The downward facing laser scanner connects to a standard tow hitch or the front of any vehicle with standard tow hooks. With using standard tow hitches and hooks, the scanner is designed to be easy to remove and adapt to any vehicle, thus eliminating the need to have a dedicated vehicle to operate the RD-M1. The unit is designed to collect millions of points at scan rates of up to 100 times per second.
Cruising at normal highways speeds, the 3-D surface scanning can cover miles of road in a short time. The collected data is automatically timestamped and stored for the next step of data management and point cloud generation. The mounted scanner captures millions of data points that are collected safely from the cab of the truck or car. Topcon points out that the driver can begin a road-surface surveying session by simply clicking the start button on their laptop computer and go.
The RD-M1 employs Collect 2.0 graphical collection software, which features an interface status bar that indicates the optimum speed for collecting road information based on the project requirements. Capturing road details at proper speed helps enable SmoothRide to deliver the best possible results.
“I like that we can collect accurate topos while driving 50 miles per hour,” stated Chris Smithson, project manager with Big Creek Construction, Lorena, TX. “We used it recently on a 3.5-mile section of Ranch Road 2838 in Mexai, TX where we were able to give the State more accurate cross sections and dirt quantities on the two-lane road and shoulders project we worked on. It saved us time and money.”
Knowing the surface details in advance allows the contractor to successfully plan for an accurate material calculation, which can help with knowing how much asphalt or milling will be required for the project. SmoothRide is considered to be especially appropriate for mainline paving or milling projects requiring long sections of road that needs resurfacing.
A feature called Memos is designed to allow operators to create balloons with messages on the map. The collected data can also be made visible in the processing software — enabling specific site conditions to be noted for future reference.
A Manage Runs feature is designed to enable operation without necessitating an internet connection. The software display’s large buttons which are intended to make using a tablet or laptop with touch screen easier. Operators can copy data collections to a USB drive, delete them from the hard drive, and add or remove them from the manager.
The RD-M1 Collect 2.0 software has a Plan Route feature that allows for the import of kml files of predetermined routes, designed to help ensure that nothing is missed during the data collection run.
“Using the map downloader, operators can be assured of having all map details visible while collecting data, without the need of an internet connection. Additionally, overlapping locations can be managed by creating areas where predefined overlaps are required for the project,” said Kriss Maas, manager of machine control, Topcon. “The detailed road surface scanning can be used to create and manage large point cloud information with our intuitive ‘Mobile Master Office’ software. The data can then be seamlessly transferred into MAGNET Office software’s ‘Resurfacing’ module to bring out the full array of software features needed to meet smoothness and cross slope requirements, while adhering to any minimum or maximum thickness specified for the job.”
The SmoothRide system can assist contractors with variable depth milling and achieve uniform thickness in paving. The system is said to eliminate the time and costs of survey work and to benefit bid and spec jobs in advance by providing more accurate surface data.
“For rehabilitation and maintenance projects, the system simplifies scanning the existing roadway surface, which we can then use for building the model for automatic machine control of our cold planers,” said Ryan Zenahlik, technology specialist for Pavement Recycling Systems, Inc., Jarupa Valley, CA.
The system is said to reduce the costs and need for survey work, and to benefit bid and spec jobs in advance by providing more accurate surface data.
“We use the 3D scanner part of SmoothRide as a survey tool to safely collect the data we need and eliminate hours of cross-section measurements,” stated John Dowalter, survey and machine control manager for Shelly and Sands, Zanesville, Ohio. “The system’s RD-M1 Scanner is great for capturing bridge approaches that sometimes have a big skew leading up to the bridge surface. That feature helped tremendously on a recent resurfacing section of I-71 between Columbus and Cleveland, which has a number of bridges that could have occupied hours of time for my crew.”
In summary, the Topcon SmoothRide system is designed to offer 3D scanning collected while driving the job-site road, which is said to replace hours of surveyor-obtained cross-section measurements. The system’s software is designed to deliver confidence throughout the paving and milling process by providing the key data needed to complete the job accurately to spec. As Topcon would phrase it, this resurfacing roadwork system fits squarely in the intersection of infrastructure and technology.
###
______________
Jeff Winke is a business and construction writer based in Milwaukee, Wis. He can be reached through jeff_winke@yahoo.com.